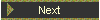
This article was written for
The
101 Association Repair and Overhaul Manual.
The Splitdorf DU-7 Generator
Repair & Overhaul
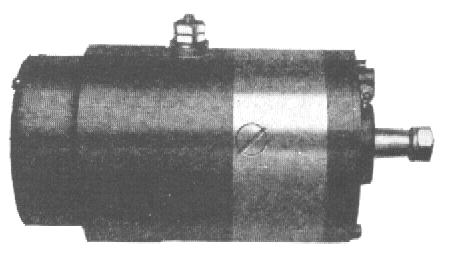
By Steve Blancard
EXACTLY WHAT GENERATOR DOES THE 101 SCOUT USE?
All 101s up until the inception of
the Auto-Lite GAS-4102 generator in 1931 used the Splitdorf DU-7, counter-clockwise
rotating generator. The DU-7 was announced by Indian as "standard equipment
on all models" in Service shot #15, dated March 5, 1928. The 101 Scout
began production on March 30, 1928, less than a month later. Service
shot #41, dated January 26th, 1930 discusses the Auto-Lite generator used
on "various models of Indian motocycles". IMPORTANT NOTE; This service
shot is apparently dated wrong. It should be dated January 26, 1931 (one
year later!). After a lengthy discussion with George Yarocki and in light
of the sequential numbering and dates of Service Shots before and after
this one, it looks as though the original Indian typist slipped by one
(very important) digit.
1931 models began production in March or April of 1931.
Considering Indian's policy of "No yearly models, but constant improvements",
and service shot #41, the last month or two of 1930 101 production may
have used the Auto-lite generator. I’ll caveat this statement with Indian's
well known practice of using up parts on hand. It is possible that DU-7s
were still used after January of 1931. Based on the available Indian and
Splitdorf documentation, all 101s built through January 26th, 1931 probably
used the Splitdorf DU-7, after which the Auto-lite-GAS 4102 would be correct.
IDENTIFICATION
Splitdorf manufactured at least 13
different motorcycle generators. The DU-7 is easily distinguished from
its predecessors by a larger cutout cover and aluminum commutator head,
visible with the cover removed.
The DU-7 cap is stamped:
SPLITDORF
MADE IN U.S.A
DU-7
All Splitdorf generators can be identified
by the model number stamped on the cutout cover. But covers were easily
lost and often replaced with whatever was available. Look for the aluminum
commutator head to be sure its a DU-7. Rotation on all DU-7s is indicated
by a small arrow stamped into the drive end of the main body, approximately
opposite the terminal post. The 101’s generator rotates counter-clockwise,
thus the arrow should be pointing to the left when looking at the pulley
end.
There are at least five DU-7 variants. These include:
DU-7, Counter-Clockwise rotation - For Indian 101
Scout and Prince.
DU-7, Counter-Clockwise rotation - For Henderson KJ,
KL.
DU-7, Clockwise rotation - For Indian Ace/401/402
DU-7, Clockwise rotation - For Cleveland (possibly marked
"DU-7C"). This one uses a unique body assembly.
DU-7H, Clockwise rotation - For Indian Chief. This model
is gear driven from the engine's timing gears. It uses a 1-1/2" long drive
shaft instead of the 1" shaft used on other models.
The only difference between the Indian
DU-7 and the Henderson DU-7 is the 1/4”-24 threaded boss located on the
drive head (behind the pulley). Many 101s I've examined have this boss
on their generator. The Prince uses this boss to attach the belt guard,
on the Scout it is simply not used. There are two possible explanations:
1) When Indian ordered the new DU-7s in late 1927 they decided to use the
same generator on both the Prince and 101 Scout. Or 2) When the Prince
was discontinued Indian had a lot of their DU-7s on hand and decided to
use them up on the 101.
TESTING AND SERVICE
Field Coils: The field coils
are wired in series. When looking at the commutator end, the left hand lead goes
to the top (positive) brush, the right to the adjustable brush. Remove the leads
from the terminals. Using an accurate ohmmeter measure the resistance through
the two coils. If they read 4-6 ohms, and are not grounded they are good.
Inspect for worn or frayed wires and coils wrapping. If the wiring is worn,
carefully cut off and solder on new leads. If you remove the field coils and
pole shoes, its a good idea to mark them first so they can be replaced in the
exact same position. When putting the pole shoes back in, it is imperative that
they be exactly parallel to the armature axis. There is only about .015" clearance between the armature and pole
shoes on either side. If the shoes are cocked at all, the armature will
strike them. In addition, as the armature heats up in use it expands, further
reducing clearance.
Above is the wiring diagram for a Splitdorf generator.
Counter clockwise rotation is on the left, clockwise
rotation is on the right.
Armature: The armature
is the heart of the generator. In order to thoroughly test it, a growler
is required. A growler is used to detect shorts in the windings. The growler
generates current in the armature by creating alternating electromagnetic
fields around it. These fields simulate those developed by the field coils
during actual operation when the armature is spinning inside the generator
body. If you do not have a growler I recommend taking your armature to
good Starter/Alternator/Generator shop for testing. However a couple
basic checks can be performed with a good multimeter;
Check for Grounds: Set your
meter to check continuity or resistance, then touch one lead to the shaft
the other to one of the commutator bars. It should show infinite or open.
Check each commutator bar all the way around the same way. Little or no
resistance indicates a grounded coil or commutator bar.
Check for Opens: Take your
leads and touch them to two different commutator bars. You should show
good continuity or .5 - 2 ohms. Check bar to bar all the way around. If
you show no continuity or very high resistance, there is probably an open
in one or more of the windings.
If these tests indicate a problem,
don't despair, the armature can be rewound. In fact the entire commutator
can be replaced if necessary. However this may be costly because they must
be done entirely by hand. Often, the armature will test O. K, but in the
long run it may be worth the extra expense of a rewind for the added reliability.
There is one other problem that may occur. Its called a "Flying Short".
This means the armature tests fine on the bench. But when it's spinning
at say 2000 rpm it shows an intermittent short caused by centrifugal force
shifting the coils and causing them to short or ground. This type of problem
can be very elusive and frustrating to isolate. If this appears to be the
case, and all other possible causes (e.g. worn brushes, frayed wiring,
dirty or rough commutator etc.) are eliminated, it's time for a rewind.
Commutator: After testing, the
commutator should be turned (trued) on a lathe and the mica insulators
(between the commutator bars) undercut with an undercutting tool about .050" deep. I follow this up with a final polish with a strip of 320 grit
wet/dry paper. Thoroughly clean the commutator of all grit and residue
afterwards.
REPLACEMENT PARTS
Bearings: Fortunately,
bearings for the DU-7 are still available. The originals are thrust type
"Torrington T-8" (commutator end),"Torrington T-13" (drive end). Modern
equivalents are available through bearing supply houses. These are known
in the trade as "magneto" bearings. It is very important to properly set
up the endplay on these bearings to .001"-.004". Endplay is adjusted by small
shims (.003" and .005" may have been used) located behind the drive
end inner race - don't loose them. I've found modern bearings may be a
few thousandths wider than originals. Often (but not always), when putting
in new bearings, removal of 1 shim gives me the proper end play. Excessive
end play can allow the armature to move side to side causing it to strike
the pole shoes.
Brushes: 1/4" x 5/16" x 1/2"
carbon. I know of no exact replacement for the originals. However brushes
designed for small electric power tools can be used. Although they are
designed for 120 volts, with some minor modification, will work very well.
The seating end of new brushes should be contoured to match the circumference
of the commutator to ensure full contact.
Hardware: All hardware on the
DU-7 is standard thread sizes (except the 1/4 - 24 threaded boss which
is not used). The two 6 x 32 end cap screws, three 8 x 32 drive head screws
and their lockwashers are blued, not nickeled as were those of previous
Splitdorf generator. The 1/4 x 20 pole shoe screws are nickeled as is the
pulley, it's nut and lockwasher and the Gits oiler. A very close replacement
for the Gits oiler is available from McMaster-Carr. The 10 x 32 terminal
post and nuts are brass. The large flat washer on the post is copper.
Felt seal: There is one felt
seal located between the commutator bearing and the commutator. This is
important to keep lubricant away from the commutator and brushes. It is 3/4" OD
x 15/32" ID x 1/8" thick.
Fuse: There is a 3 amp fuse located on the commutator
head to protect the field coils. Carry a couple spares in your toolkit.
EXTERIOR FINISH
Generator bodies were plated to ensure
good electrical contact with the mounting bracket. I've observed some plated
with tin, others with nickel. This is rarely seen on surviving generators
due to the rapid deterioration of the plating. However, it is readily visible
in period photos and Splitdorf literature. The ends of the body were then
painted gloss black, approximately 1.2" from the commutator end and .5"
from the drive end, leaving a plated center stripe where the mounting clamp
attaches. The cutout cover and drive head were also painted gloss black.
CUTOUTS
The cutout relay is a device used
to prevent the battery from discharging back through the generator when
the armature is not rotating fast enough to produce sufficient current.
The DU-7 used an improved electrical cutout, located under the end cover.
Don't assume that any Splitdorf generator with an electrical cutout is
a DU-7. The earlier "A-10" electrical cutout used on DU-5s is not the same
as the DU-7's cutout. Indian service shot #35, dated November 5th, 1929
provides detailed adjustment procedures for the DU-7 cutout and is an excellent
reference. Contact points should be set at .015 - 020". The shunt windings
of early DU-7 cutouts were prone to vibration damage. In late 1929 Splitdorf
offered free replacement of the defective cutouts with a more durable unit.
The replacements were all stamped on the base with a date. The early cutouts
were not dated. One final note on cutouts; Other than cleaning and adjusting
the points, follow the old proverb "If it ain't broken, don't fix it".
They are the Achilles heel of the generator and are easily damaged.
ADJUSTING CURRENT OUTPUT
Adjustment is easy, however the actual
output must be tailored to each motorcycle. Amperage is increased by loosening
2 screws clamping the adjustable brush holder, then moving it in the direction
of armature rotation (clockwise looking at the commutator end), then retighten
the screws. Ideally, the generator should provide a positive charge of
1 to 1-1/2 amps to keep the battery charged (just like a trickle charger).
If most of your riding is during daylight hours, you'll probably want to
adjust the generator output with all lights off. However, if you do a lot
of night riding, adjusting the output with the lights on, and always riding
with them on may be preferable. If available, use a high quality ammeter
when adjusting output current. While adequate for daily use, the original
equipment ammeter is not accurate enough for precision adjustments. If
the generator does not provide sufficient current to meet demand, current
will be drawn from the battery as well as that supplied by the generator.
Adjust generator output to meet your electrical system's needs - but no
more.
When properly restored, the Spltidorf DU-7 will
provide many more years of reliable service. Good luck!
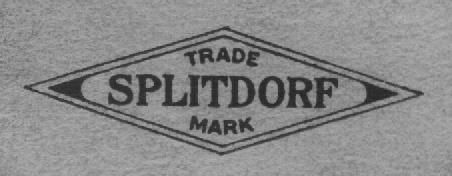
|